ВВЕДЕНИЕ В ТЕХНОЛОГИЮ Принцип работы магнитно-импульсного дефектоскопа основан на изучении затухания во времени вихревых токов в металлических трубах, индуцированных электромагнитным импульсом.
Для возбуждения вихревых токов внутри концентрических труб соосно помещается электромагнитная катушка, являющаяся частью прибора, через которую пропускаются вихревые токи (рис 5.1). В случае прямоугольного импульса возбуждение вихревых токов происходит дважды, на переднем и заднем фронте импульса. Отклик обычно замеряется после затухания заднего фронта импульса, так как данный процесс хорошо изучен и его проще учесть при последующей интерпретации. Амплитуда электромагнитного импульса задается таким образом, чтобы все переходные процессы на переднем фронте прекращались еще до получения отклика. При одинаковой амплитуде импульса вихревые токи затухают дольше в трубах с более толстой стенкой. Наличие дефектов и коррозий приводит к более высокой скорости затухания индуцированных токов, т.к. эти токи обтекают эти дефекты или прерываются ими. Коррозия трубы вызывает уменьшение толщины ее стенки, в результате чего увеличивается сопротивление. Для выявления дефектов скважинных барьеров анализируется скорость затухания вихревых токов. Благодаря дальнодействию электромагнитных полей появляется возможность анализировать несколько расположенных соосно труб различного диаметра, которые исследуются за один спуск. Датчик с катушкой способен эффективно сканировать трубы диаметром до трех четвертей своей длины.
Чтобы иметь возможность сканировать барьеры различного типа, прибор обычно оборудуется несколькими катушками разной длины, каждая из которых предназначена для трубы соответствующего диаметра. Соосно расположенные генераторная и приемная катушки располагаются вместе, с тем чтобы исключить ложные сигналы, которые могут интерпретироваться как дефекты.
Затухающие вихревые токи наводят электродвижущую силу (ЭДС) в приемной катушке, по величине которой можно судить о скорости их затухания.
Рис 5.1. Типичный цикл измерения для прибора с двумя зондами. Ток на генераторной катушке показан синей кривой, а измеряемая ЭДС на приемной катушке – зеленой.
Регистрируемая датчиком ЭДС пропорциональны величине продольной составляющей электромагнитного поля в месте расположения датчика: Ureciever = Ccoil Eφ (r,z,t) (5.1) где Ccoil – коэффициенты, характеризующие геометрию и электромагнитные параметры генераторной и приемной катушек, которые определяются на основании калибровочных данных завода-изготовителя. Эволюция магнитного поля в общем случае описывается уравнениями Максвелла: ∂t∂trot(E)=–∂—B;div(D)=ρ; rot(H)=j+∂—D; div(B)=0, (5.2) где E⃗ – напряженность электрического поля, B⃗ – магнитная индукция, D⃗ – электрическая Уравнение 5.2 описывает эволюцию тангенциальной компоненты электрического поля в случае двумерного распределения параметров исследуемой среды – по радиальному (r) и по аксиальному (z) направлениям. Таким образом, регистрируемый прибором отклик зависит от магнитной проницаемости, проводимости, силы генерируемого катушкой магнитного поля, диаметра и толщины труб, а также от конструктивных решений используемого зонда (габаритов, силы тока и т.д.).
Технические характеристики прибора EmPulse Прибор EmPulse может включать в себя до трех электромагнитных датчиков (короткий, средний и длинный). Каждый датчик оборудован двумя катушками – генераторной и индукция, ρ – плотность электрического за-приемной. Обе катушки располагаются кон- ряда, H⃗ - напряженность магнитного поля,
центрически вокруг композитного стержня j – плотность тока. Фактически, компоновка труб представляет сбой слоистую аксиально-симметричную систему. Поскольку сканирование производится продольным зондом, то уравнения Максвелла можно свести к одному уравнению:
 где z – расстояние по стволу, r – радиальное расстояние от скважины, σ (r, z) – электро- проводность, � (r, z) – магнитная проницаемость, Eφ (r, z) – продольная составляющая электромагнитного поля, j (r, z) – плотность тока генераторной катушки, and �0 – магнитная проницаемость вакуума. (рис. 5.2). Прибор EmPulse способен выявлять и анализировать поперечные и продольные дефекты в каждом из первых трех коаксиальных металлических барьеров. Прибор показал свою эффективность в исследовании труб, изготовленных из различных сортов стали, включая высокохромистые сплавы, и обладающих разной массой. Его титановый корпус позволяет производить исследования в агрессивных средах с содержанием сероводорода до 30% (рис. 5.2).
Short Sensor (5")
 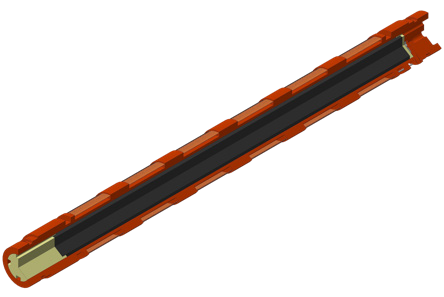 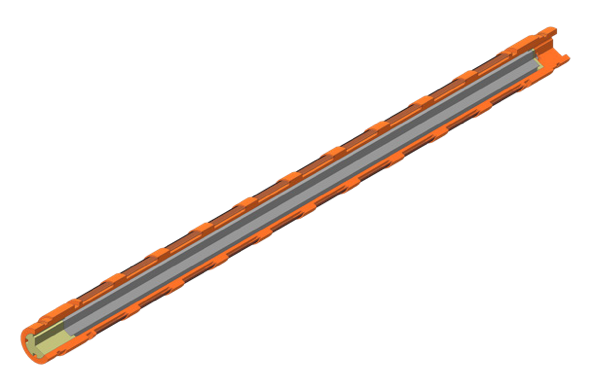 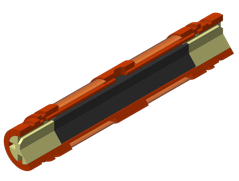 Long Sensor (19")Medium Sensor (13")
Рис. 5.2. Конструкция приборов EmPulse-2 и EmPulse-3.
Технические характеристики приведены в Таблице 5.1.
Таблица 5.1. Технические характеристики прибора EmPulse. Параметр | Значение | Диапазон рабочих температур | -20…150 °С (-4…302 °F) | Максимальное рабочее давление | 100 МПа (14 500 фунт/дюйм2) | Максимальная концентрация H2S | 30% | Максимальная толщина стенки трубы | 38 мм (1.5") | Диаметр трубы | 51–381 мм (2"–15") | Рекомендуемая скорость движения прибора | 2–4 м/мин (6–12 фут/мин)
| Время автономной работы | 48 ч |
Концепция приборов Indigo
Основной отличительной чертой приборов EmPulse с интерфейсом Indigo является наличие одножильной шины Indigo 2.0, по которой подается питание на прибор и осуществляется обмен данными. Это дает возможность комбинировать различные модули (MID, Navigator, Hex, PT, ReCap, SNL и т.д) в одной связке и в необходимой последовательности. Одножильная шина позволяет пользователю получать информацию о подсоединенных приборах, их текущей конфигурации и протяженности интервалов исследования, включать и выключать регистрирующие датчики, загружать требуемый сценарий исследования (в автономном режиме), а также считывать данные непосредственно со связки приборов через аппаратный адаптор и комплексного программного обеспечения Indigo Suite. В приборах EmPulse реализована функция автоматической самодиагностики. Алгоритмы работы приборов могут задаваться таким образом, чтобы продолжительность и период повторения импульсов были индивидуальными для каждого прибора. Для предотвращения взаимных помех существует возможность синхронизации нескольких модулей в одной связке . Существуют две модификации прибора EmPulse, разработанные для скважин различной конструкции: Indigo EmPulse-2 и EmPulse-3. Прибор EmPulse-2 предназначен для сканирования первого и второго металлического барьера диаметром до 9-5/8", в то время как EmPulse-3 рассчитан на трубы большего диаметра и способен выявлять дефекты в трубах диаметром до 15". Эти модули могут применяться совместно или отдельно. В случае их совместного использования эти модули позволяют производить оценку толщины стенки первой, второй и третьей концентрически расположенных труб за один проход прибора. Полный цикл последовательности генерации и считывания для прибора EmPulse-2 составляет 0,8 сек, для модуля EmPulse-3 – 1,2 сек, а при их совместном использовании – 2 сек. Использование модулей отдельно друг от друга является предпочтительным, так как в этом случае становится возможным производить запись данных на большей скорости – 4 м/мин, в то время как при их совместном одновременном использовании рекомендуемая скорость ограничивается 1-2 м/мин.
Данные о чувствительности модуля EmPulse-2 к дефектам приводятся в Таблице 5.2.
Таблица 5.2. Чувствительность модуля EmPulse-2 к дефектам.
Диаметр труб (дюйм) | Толщина |
| Минимальный размер сквозного дефекта в 1 барьере |
| Минимальный размер сквозного дефекта во 2 барьере |
|
| 1 барьер | 2 барьер |
|
|
|
| 2 ⅞ | + |
| 15 мм | 0.6" |
|
| 3 ½ | + |
| 20 мм | 0.8" |
|
| *3 ½ (нерж. сталь)* | + |
| 7 мм | 0.3" |
|
| 4 ½ | + |
| 25 мм | 0.9" |
|
| 5 ½ | + |
| 40 мм | 1.5" |
|
| 7 | + |
| 50 мм | 2" |
|
| 9 ⅝ | + |
| 65 мм | 2.5" |
|
| 13 ⅜ | + |
| 90 мм | 3.5" |
|
| *2 ⅞ + 5 ½* | + | + | 20 мм | 0.7" | 65 мм | 2.5" | *3 ½ + 5 ½* | + | + | 20 мм | 0.8" | 65 мм | 2.5" | *3 ½ + 7* | + | + | 20 мм | 0.8" | 68 мм | 2.7" | *4 ½ + 7* | + | + | 25 мм | 0.9" | 70 мм | 2.8" | *5 ½ + 7* | + | + | 41 мм | 1.6" | 100 мм | 4" | *3 ½ + 9 ⅝* | + | + | 20 мм | 0.8" | 100 мм | 4" | *4 ½ + 9 ⅝* | + | + | 25 мм | 0.9" | 100 мм | 4" | *5 ½ + 9 ⅝* | + | + | 41 мм | 1.6" | 115 мм | 4.5" | 7 + 9 ⅝ | + | + | 53 мм | 2.1" | 115 мм | 4.5" | *4 ½ + 7 + 9 ⅝* | + | + | 25 мм | 0.9" | 86 мм | 3.4" | *3 ½ + 9 ⅝ + 13 ⅜* | + | + | 20 мм | 0.8" | 140 мм | 5.5" | *4 ½ + 9 ⅝ + 13 ⅜* | + | + | 25 мм | 0.9" | 140 мм | 5.5" | *7 + 9 ⅝ + 13 ⅜* | + | + | 53 мм | 2.1" | 140 мм | 5.5" | *Двухрядная компоновка 3 ½ + 9 ⅝* | +
| +
| 25 мм
| 1"
| 152 мм
| 6"
|
Точность измерения толщины стенки | Значение | 1 барьер | ±3.5% (±0,01" или ± 0.25 мм для НКТ 3 ½'' с толщиной стенки 7 мм) | 2 барьер | ±6% (±0,03" или ± 0.75 мм для колонны 9 ⅝'' с толщиной стенки 12 мм) |
Данные о чувствительность модуля EmPulse-3 к дефектам приведены в Таблице 5.3.
Таблица 5.3. Чувствительность модуля EmPulse-3 к дефектам.
Диаметр труб (дюйм) | Минимальный размер отверстия в 1 барьере |
| Минимальный размер отверстия во 2 барьере |
| Минимальный размер отверстия в 3 барьере |
| 7 | 2" | 51 мм |
|
|
|
|
| 9 ⅝ | 2.5" | 65 мм |
|
|
|
|
| 13 ⅜ | 3.5" | 89 мм |
|
|
|
|
| 2 ⅞ + 7 | 0.7" | 18 мм | 2.7" | 69 мм |
|
|
| 3 ½ + 7 | 0.8" | 20 мм | 2.7" | 69 мм |
|
|
| 4 ½ + 7 | 0.9" | 23 мм | 2.8" | 71 мм |
|
|
| 5 ½ + 7 | 1.6" | 41 мм | 4" | 102 мм |
|
|
| 2 ⅞ + 9 ⅝ | 0.7" | 18 мм | 3" | 76 мм |
|
|
| 3 ½ + 9 ⅝ | 0.8" | 20 мм | 4" | 102 мм |
|
|
| 4 ½ + 9 ⅝ | 0.9" | 23 мм | 4" | 102 мм |
|
|
| 5 ½ + 9 ⅝ | 1.6" | 41 мм | 4.5" | 114 мм |
|
|
| 7 + 9 ⅝ | 2.1" | 53 мм | 4.5" | 114 мм |
|
|
| 2 ⅞ + 13 3/8 | 0.7" | 18 мм | 6" | 152 мм |
|
|
| 3 1/2 + 13 3/8 | 0.8" | 20 мм | 6" | 152 мм |
|
|
| 4 1/2 + 13 3/8 | 0.9" | 23 мм | 6" | 152 мм |
|
|
| 5 1/2 + 13 3/8 | 1.6" | 41 мм | 6" | 152 мм |
|
|
|
Диаметр труб (дюйм) | Минимальный размер отверстия в 1 барьере |
| Минимальный размер отверстия во 2 барьере |
| Минимальный размер отверстия в 3 барьере |
| 7 + 13 3/8 | 2.1" | 53 | 6" | 152 мм |
|
|
| 9 ⅝ + 13 ⅜ | 2.6" | 66 мм | 6" | 152 мм |
|
|
| 2 ⅞ + 5 ½ + 7 | 0.7" | 18 мм | 3" | 76 мм | 6" | 152 мм |
| 3 1/2 + 5 ½ + 7 | 0.8" | 20 мм | 3" | 76 мм | 6" | 152 мм |
| 4 1/2 + 5 ½ + 7 | 0.9" | 23 мм | 3" | 76 мм | 6" | 152 мм |
| 2 ⅞ + 5 ½ + 9 ⅝ | 0.7" | 18 мм | 3" | 76 мм | 7" | 178 мм |
| 3 1/2 + 5 ½ + 9 ⅝ | 0.8" | 20 мм | 3" | 76 мм | 7" | 178 мм |
| 4 1/2 + 5 ½ + 9 ⅝ | 0.9" | 23 мм | 3" | 76 мм | 7" | 178 мм |
| 2 ⅞ + 7 + 9 ⅝ | 0.7" | 18 мм | 3.3" | 84 мм | 7" | 178 мм |
| 3 ½ + 7 + 9 ⅝ | 0.8" | 20 мм | 3.3" | 84 мм | 7" | 178 мм |
| 4 ½ + 7 + 9 ⅝ | 0.9" | 23 мм | 3.4" | 86 мм | 7" | 178 мм |
| 5 ½ + 7 + 9 ⅝ | 1.6" | 41 мм | 4.9" | 124 мм | 7" | 178 мм |
| 2 ⅞ + 5 ½ + 13 ⅜ | 0.7" | 18 мм | 3" | 76 мм | 7.5" | 191 мм |
| 3 1/2 + 5 ½ + 13 ⅜ | 0.8" | 20 мм | 3" | 76 мм | 7.5" | 191 мм |
| 4 1/2 + 5 ½ + 13 ⅜ | 0.9" | 23 мм | 3" | 76 мм | 7.5" | 191 мм |
| 2 ⅞ + 7 + 13 ⅜ | 0.7" | 18 мм | 3.2" | 81 мм | 7.5" | 191 мм |
| 3 1/2 + 7 + 13 ⅜ | 0.8" | 20 мм | 3.2" | 81 мм | 7.5" | 191 мм |
| 4 1/2 + 7 + 13 ⅜ | 0.9" | 23 мм | 3.4" | 86 мм | 7.5" | 191 мм |
| 5 1/2 + 7 + 13 ⅜ | 1.6" | 41 мм | 4.8" | 122 мм | 7.5" | 191 мм |
| 2 7/8 + 9 ⅝ + 13 ⅜ | 0.7" | 18 мм | 4.5" | 114 мм | 7.5" | 191 мм |
| 3 ½ + 9 ⅝ + 13 ⅜ | 0.8" | 20 мм | 5.5" | 140 мм | 7.5" | 191 мм |
| 4 ½ + 9 ⅝ + 13 ⅜ | 0.9" | 23 мм | 5.5" | 140 мм | 7.5" | 191 мм |
| 5 ½ + 9 ⅝ + 13 ⅜ | 1.6" | 41 мм | 5.5" | 140 мм | 8" | 203 мм |
| 7 + 9 ⅝ + 13 ⅜ | 2.1" | 53 мм | 5.5" | 140 мм | 8" | 203 мм |
|
РЕГИСТРАЦИЯ ДАННЫХ
Короткий датчик модуля EmPulse-2 генерирует короткие низкоамплитудные электромагнитные импульсы, намагничивающие главным образом первый барьер, а затем регистрирует временные спады намагниченности. Датчик широко используется для контроля технического состояния насосно-компрессорных труб, но может также применяться в аналогичных целях в колоннах обсадных труб диаметром до 5". Минимальный размер обнаруживаемых дефектов определяется размером датчика, который составляет примерно 0,9". В случаях, когда дефект по своим размерам превышает минимальный, регистрируется уменьшение как амплитуды, так и времени спада намагниченности по сравнению с номинальным. Соответственно, когда в радиус сканирования прибора попадает дополнительный объем металла, например, муфта, спад намагниченности происходит дольше номинального спада. Таким образом, амплитуда магнитного поля, зарегистрированного в зоне муфты, будет выше номинала на всем протяжении спада (см. рис 5.3). Спад намагниченности начинает отклоняться от номинального не с самого начала, а спустя 0,003 сек после начала регистрации спада. Средний датчик EmPulse-2 оптимизирован под сканирование металлических барьеров диаметром от 5" до 13" для первого барьера и до 9-5/8" для второго барьера. Этот датчик генерирует электромагнитные импульсы с большей амплитудой, чем у короткого датчика. Менее чем за 0,05 секунды (рис. 5.4) происходит равномерный спад намагниченности по всему второму барьеру и его компонентам,
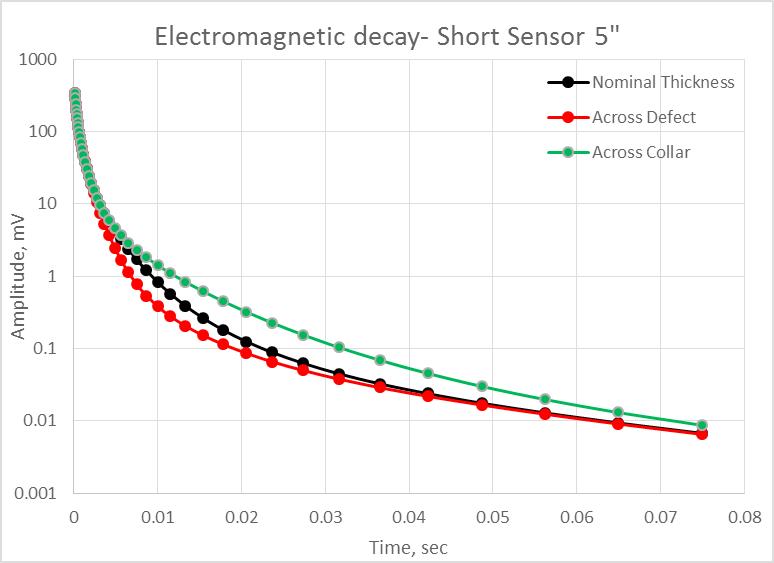 Рис. 5.3. Электромагнитные спады, зарегистрированные коротким 5" датчиком в металлическом барьере 4-½" для интервала со стенкой номинальной толщины (черная кривая), зоны 10% коррозии (красная кривая) и муфты (зеленая кривая).
включая муфты. Отклонение спада от номинала напротив дефекта начинает происходить cпустя 0.05 сек после начала регистрации, что значительно позже, чем в случае нахождения дефекта в первом барьере (рис. 5.3). Данное явление используется для в определения места коррозий, встречающихся в первом, втором и третьем барьерах (рис. 5.4). Длинный датчик EmPulse-3 генерирует долгие высокоамплитудные электромагнитные импульсы и регистрирует более длительные спады намагниченности. Регистрируемые отклики отражают состояние первого, второго и третьего барьеров диаметром до 14". Отклонения зарегистрированных спадов намагниченности в интервалах напротив муфт и дефектов в третьем барьере начинаются позже, чем в первом и втором барьерах (рис. 5.5). Наличие коррозии или дефекта ускоряет затухание, в то время как в зоне напротив муфт происходит замедление магнитного спада. Важно отметить, что коррозии и муфты на спадах намагниченности проявляются на разных временах, т.к. отклонение замеренного электромагнитного спада от номинального в зоне коррозии происходит раньше, чем в зоне муфты. Коррозия проявляется на данных спада намагниченности каждого барьера в тот же самый интервал времени, в котором регистрируется отклик от соответствующей муфты. Данные электромагнитного спада, регистрируемые 5" датчиком оцифровываются по 42 каналам. Средний 13" датчик регистрирует спад по 51 каналу, в то время как длинный 19" датчик, обладая наибольшим временем наблюдения, производит оцифровку спада по 91 каналу. Таким образом, в общей сложности прибором осуществляется запись по 181 каналу за один спуск в скважину.
Рис. 5.4. Электромагнитные спады, зарегистрированные средним 13" датчиком в НКТ 4-½" для интервала со стенкой номинальной толщины (черная кривая), зоны 10% коррозии (красная кривая) и муфты колонны 9-5/8" (зеленая кривая).
Процедура регистрации данных Исследование EmPulse может проводиться как во время спуска, так и во время подъема, как в остановленной, так в работающей скважине. Тем не менее, рекомендуется производить запись на подъеме в остановленной скважине, т.к. скорость движения прибора при этом более равномерна. Несмотря на отсутствие каких-либо особых требований к режиму работы скважины, следует отметить, что в случаях, когда первый металлический барьер имеет малый диаметр или же скважина является добывающей и работает с высоким дебитом, прибор может двигаться неравномерно, что в свою очередь может сказаться на качестве замеренных данных. Любое спущенное в скважину электрическое оборудование, такое как ЭЦН, катодная защита, датчики температуры и давления, также может повлиять на работу прибора и записываемые данные. В связи с этим, перед исследованием необходимо отключить все скважинное оборудование от источника питания. Внизу представлена типовая схема исследования многобарьерной скважины. На рис. 5.7 представлен весь набор данных комплексного прибора EmPulse: данные с короткого 5" датчика представлены на панели SS, со среднего датчика – на панели MS для модуля EmPulse-2. Данные с длинного датчика представлены на панели данных LS для модуля EmPulse-3. На рис. 5.7 также показано увеличенное изображение каротажных кривых, записанных длинным 19" датчиком, на которых видны муфты каждого из трех барьеров скважин-
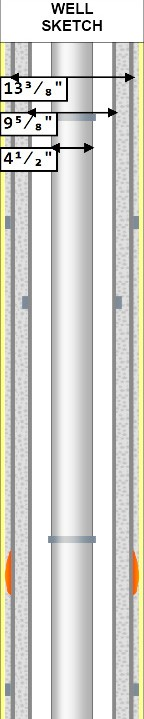 Рис. 5.5. Электромагнитные спады, зарегистрированные длинным датчиком EmPulse-3 в НКТ 4-½" и колонне 9-5/8" для интервала со стенкой номинальной толщины (черная кривая), зоны 10% коррозии (красная кривая) и муфты колонны 13-3/8" (зеленая кривая).
ной подвески. Это свидетельствует о том, что каждая каротажная кривая содержит в себе совокупную информацию о всех подвергшихся сканированию барьерах. Поэтому для количественной оценки степени коррозии в скважине недостаточно использовать только данные конкретного датчика или временного канала, но необходимо осуществлять совместный анализ всей совокупности данных, полученных со всех датчиков.
ОБРАБОТКА ДАННЫХ
Применение моделирования в магнитно-импульсной дефектоскопии
В магнитно-импульсной дефектоскопии толщина стенок металлических труб определяется с применением математического моделирования и последующим сравнением откликов, зарегистрированных в скважине прибором EmPulse, c модельными откликами для скважины определенной конструкции. Зарегистрированные спады намагниченности могут быть использованы не только для определения толщины каждого металлического барьера скважины, но также и для определения электромагнитных параметры труб – магнитной проницаемости и электромагнитной проводимости. Одним из преимуществ данного метода является то, что он является более гибким при адаптации модели к любым скважинам, имеющиминдивидуальныеособенности конструкции, металлического барьера и т.д. Прибор EmPulse регистрирует совокупность сигналов от всех металлических барьеров в скважине, включая данные о воздействии, оказываемом соседними барьерами. В связи с этим, для определения свойств материала, из которого изготовлены трубы, и точного расчета толщины их стенок модель должна учитывать индивидуальные отклики от всех барьеров. Данная задача решается при помощи двухмерного симулятора EmPulse, основанного на численном решении осесимметричного уравнения Максвелла (2), в котором используется моделирующий отклики датчика алгоритм. Симулятор учитывает геометрию прибора с центраторами и моделирует отклики одновременно от нескольких датчиков в двух измерениях – вдоль ствола скважины и в радиальном направлении (рис. 5.8). На рис. 5.9 показано, с какой степенью точности показания прибора могут быть адаптированы к двухмерной численной модели.
Определение толщины стенки
Для определения толщины стенок исследуемых барьеров необходимо сопоставить модельный спад намагниченности с замеренным спадом путем последовательного изменения параметров электрической проводимости, магнитной проницаемости и толщин барьеров для каждой глубины. Сопоставление модельных спадов с регистрируемыми производится для каждого из датчиков в отдельности(рис. 5.10). Моделирование EmPulse представляет собой многопараметрический математический процесс. На основании многочисленных лабораторных исследований можно сделать вывод, что значения электрической проводимости и магнитной проницаемости остаются более или менее постоянными на всем протяжении трубы (стандартной длины 33 фута) и зависят от сорта стали и степени ее механического старения. Исходя из этого, процедура моделирования может выполняться в несколько этапов. На
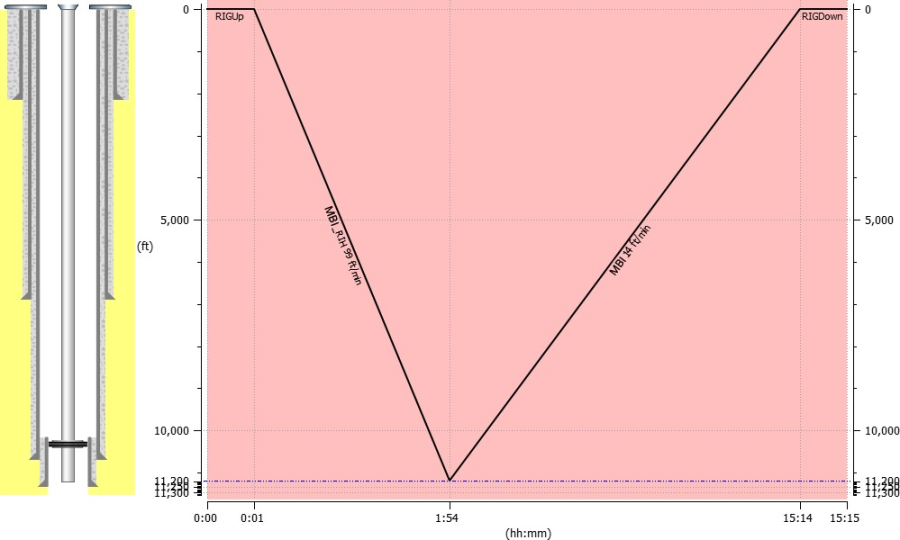 Рис. 5.6. Типовая процедура исследования EmPulse со спуском прибора до нижней границы интервала исследования и записью на подъеме со стабильной скоростью не более 6 м/мин до верхней границы интервала.
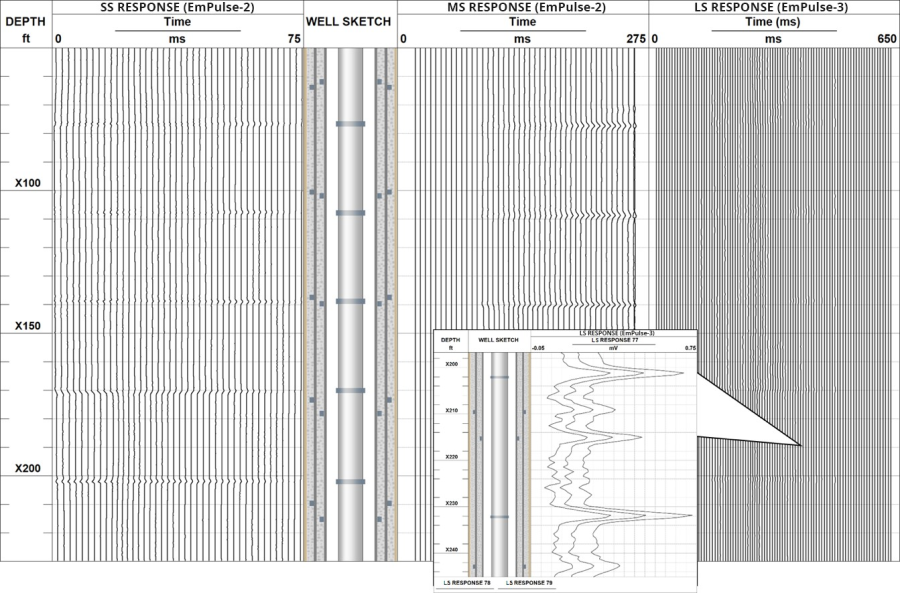 Рис. 5.7. Исходные данные комплексного прибора EmPulse. На панели короткого датчика (EmPulse-2) представлены спады намагниченности, оцифрованные 42 временными каналами 5" датчика, на панели среднего датчика (EmPulse-2) – 51 каналом 13'' датчика (MID-2) и на панели длинного датчика (EmPulse-3) – 91 каналом 19'' датчика. Увеличенный фрагмент демонстрирует изменение отклика напротив муфт первого, второго и третьего барьеров.
Radial Distance, mmRadial Distance, mmMagnetic fieldElectrical current, a.u.A
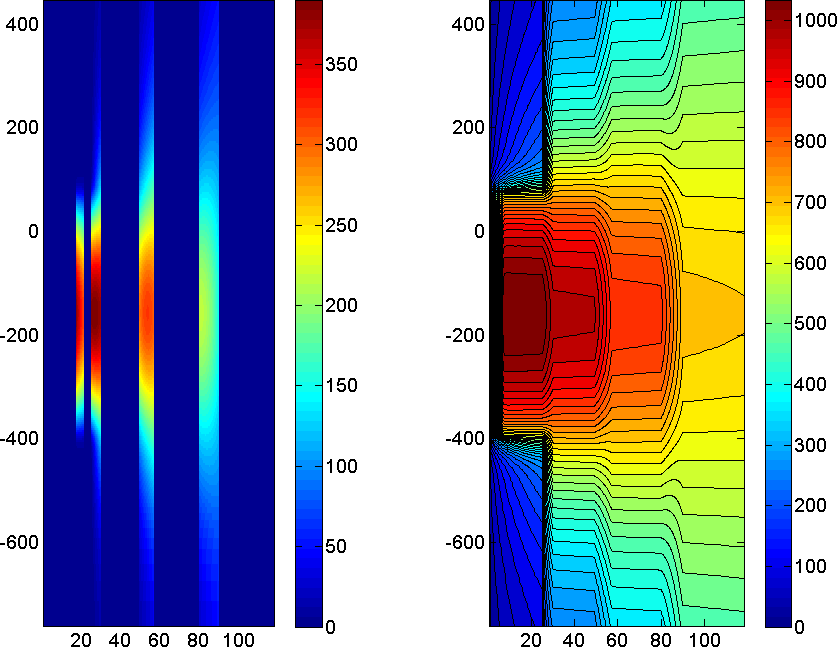 BElectrical current, a.u.Magnetic fieldRadial Distance, mmRadial Distance, mm Рис. 5.8. Двухмерная модель EmPulse. Результат моделирования распределения электрических токов (слева) и магнитного поля (справа), индуцированные и замеренные приборами EmPulse-2 и EmPulse-3 в НКТ и двух обсадных колоннах.
первом этапе алгоритм анализирует отклики датчика на всех глубинах с применением коррелированных по глубине линий трендов и распознает трубные муфты во всех барьерах. Затем он разбивает каждый из барьеров на несколько отрезков, расположенных между муфтами, и создает список скважинных интервалов, в которых имеются все барьеры, но отсутствуют муфты. На следующем этапе алгоритм анализирует все спады для каждого из отрезков, выбирает статистически репрезентативные спады и, исходя из допущения, что электрическая проводимость и магнитная проницаемость являются постоянными по всему отрезку трубы (хотя их значения могут различаться для разных барьеров), изменяет эти два параметра и толщину стенки трубы до получения оптимального соответствия с откликом датчика (рис. 5.11). На заключительном этапе данный алгоритм создает профили толщины стенки, электрической проводимости и магнитной проницаемости для каждого из трех барьеров (рис. 5.11). Этот алгоритм получил название адаптации в реальном времени или Real-Time Fitting (RTF), т.к. с его помощью моделируются отклики и производится адаптация модельных и измеренных откликов непосредственно в процессе расчета толщин. Алгоритм RTF является автокалибруемым и учитывает любые сочетания концентрически расположенных труб без необходимости введения данных о сорте стали, коэффициенте старения и особенностях конструкции, т.к. сорт стали определяется по произведению магнитной проницаемости и электрической проводимости (μ∙σ) с введением этих данных в процесс
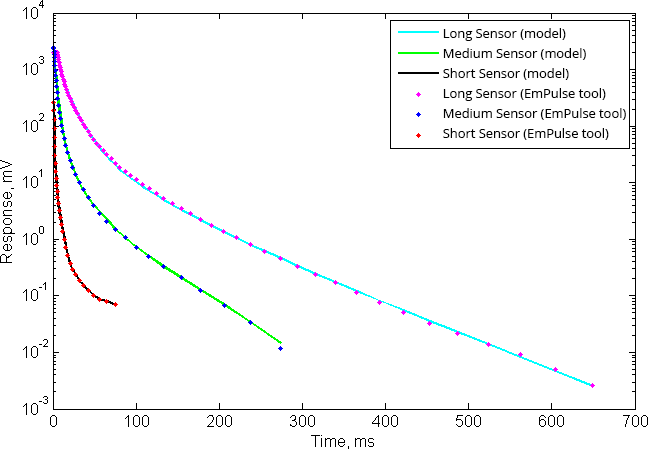 Рис. 5.9. Представлены результаты адаптации замеренных (пунктирные линии) и моделируемых (сплошные линии) спадов намагниченности для всех трех сенсоров прибора EmPulse.
Рис. 5.10. Результаты моделирования EmPulse для первого барьера (колонна 7") с оптимальным соответствием, полученным при толщине стенки 7,5 мм (зеленая линия).
моделирования на отдельной панели данных. Это зачастую позволяет распознать трубы, изготоленные из нестандартных материалов, таких как стальные сплавы, содержащие хром или магний в различных концентрациях. Cканируемые трубы могут иметь остаточную намагниченность по следующим причинам:
- Работа электрического скважинного оборудования.
- Механические нагрузки на скручивание, изгиб и т.д.
- Трение бурильной трубы о колонну во время бурения.
- Воздействия в процессе транспортировки и хранения.
Остаточная намагниченность значительно искажает регистрируемый сигнал, особенно в случае увеличения скорости движения прибора в скважине. Подобные искажения достаточно хорошо фильтруются, т.к. они производят одинаковый эффект на всех каналах прибора. На поздних временах магнитного спада, когда вихревые токи затухают, регистрируемый прибором EmPulse сигнал содержит лишь эту остаточную намагниченность. Симулятор EmPulse автоматически вычитает этот вклад от магнитной помехи в отклик прибора.
Рис. 5.11. Результаты численного моделирования для определения толщины стенки. Черные пунктирные линии в трубах «НКТ» и «ОБСАДНАЯ КОЛОННА» обозначают номинальную толщину стенок НКТ и обсадной колонны соотвественно, зеленые сплошные линии в колонках «Толщина» обозначают модельную толщину стенок НКТ и обсадной колонны по данным зарегистрированного отклика EmPulse. Отмеченные синим цветом участки означают зоны, где модельная толщина превышает номинальную, а коричневым – те зоны, где модельная толщина ниже номинальной. Значения электрической проводимости (σ) и магнитной проницаемости (µ) приводятся в соответствующих колонках для типов стали каждой трубы НКТ или обсадной колонны.
ТЕСТИРОВАНИЕ ТЕХНОЛОГИИ В ХОДЕ ЛАБОРАТОРНЫХ ИССЛЕДОВАНИЙ Была осуществлена обширная программа лабораторных исследований, с целью определения характеристик прибора EmPulse, его регистрируемого отклика на дефекты в первом, втором и третьем скважинных барьерах. С помощью подобных исследований можно оценивать качество, чувствительность и надежность датчиков, электроники прибора и технологии в целом путем моделирования вариантов конструкции скважины с различными сочетаниями типов спущенных труб. Тест 1. Определение минимальной потери металла для каждого барьера в конструкциях с двумя барьерами Ниже приводится описание процедуры лабораторного испытания, проведенного с целью определения минимальной потери металла в конструкциях скважин с двумя барьерами. В ходе испытания была применена двухбарьерная система, состоящая из труб диаметром 3-½" и 9-5/8" длиной по 3 метра каждая, с проточенными по окружностями желобками, расположенными на расстоянии 0,75 м друг от друга, имитирующими постепенную потерю металла.
!worddavb9db6492b00d6cd1f8206b40e4890356.png|height=422,width=312!Рис. 5.12a. Результаты лабораторных исследований: согласованное изменение измеренной и номинальной толщины стенок первого и второго барьеров (3-½" и 9-5/8"). Смоделированные толщины обеих труб отображены зеленой и синей кривыми с учетом влияния изменения толщины первого барьера на расчет толщины второго.
!worddav71a95bbf048541c993700a41567cc2e2.png|height=408,width=308!Рис. 5.12b. Результаты лабораторных исследований: обратно пропорциональное изменение измеренной и номинальной толщины стенки труб диаметром 3-½" и 9-5/8". Смоделированные толщины обеих труб отображены зеленой и синей кривыми с учетом влияния изменения толщины первого барьера на расчет толщины второго.
На рис. 5.12a показаны результаты лабораторных испытаний для труб обоих диаметров (3-½" и 9-5/8") с уменьшением толщины стенки в зависимости от глубины. На рис. 5.12b показаны результаты лабораторных испытаний для системы, при которой толщина стенки трубы 3-½" увеличивалась, в то время как толщина трубы 9-5/8" уменьшалась. Расхождение между смоделированными и фактическими толщинами было менее 0,4 мм (6%) для первого барьера и менее 0,8 мм (8%) для второго. Тест 2. Оценка размеров наименьшего дефекта в третьем барьере (труба 13-3/8") Данное исследование проводилось с целью проверки способности прибора выявлять дефекты в третьем барьере, который обычно представлен кондуктором 13-3/8", а также для демонстрации чувствительности прибора к дефектам в трубах большого диаметра в целом и его способности определять толщину стенок первых трех барьеров. Ниже представлено описание одной из лабораторных установок. Компоновка состояла из трубы 3-½", трубы 9-5/8", представляющей промежуточную колонну, и трубы 13-3/8". В последней трубе обсадной колонны было просверлено отверстие диаметром 7-½", что эквивалентно равномерной потере металла, составляющей 8,8%. На рис. 5.13 приводятся результаты лабораторного исследования. Модельная кривая толщи-
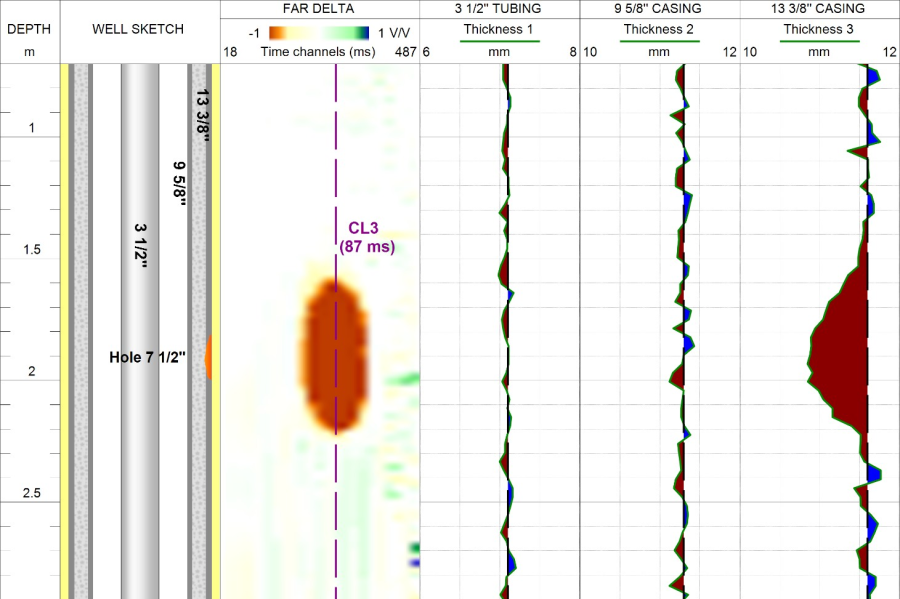 Рис. 5.13. Результаты лабораторных исследований прибором EmPulse-3: зарегистрированный дефект в третьем барьере (колонна 13-3/8").
ны стенки трубы 13-3/8" однозначно показывает наличие дефекта. Расчетная потеря металла в районе местонахождения дефекта составила 6,7%. Во временном интервале дефекта не отмечено каких-либо значительных отклонений от откликов первого и второго барьеров. Тест 3. Оценка размеров наименьшего дефекта в трубе 13-3/8" при наличии колонны трубы 18" Еще одно лабораторное исследование проводилось с целью проверки способности прибора EmPulse выявлять дефекты во втором барье- ре трехбарьерной конструкции и определять толщину стенок первых трех барьеров. Тестовая модель состояла из вставленных друг в друга труб диаметром 9-5/8", 13 3/8" и 18". В трубе 13-3/8" было просверлено отверстие диаметром 7-½", имитирующее равномерную потерю металла, составляющей 8,8%. Задача заключалась в выявлении дефектов в первых трех барьерах. На рис. 5.14 показаны результаты лабораторного исследования. Дефект во втором барьере (труба 13-3/8") фиксируется как потеря металла, составляющая 6,7%.
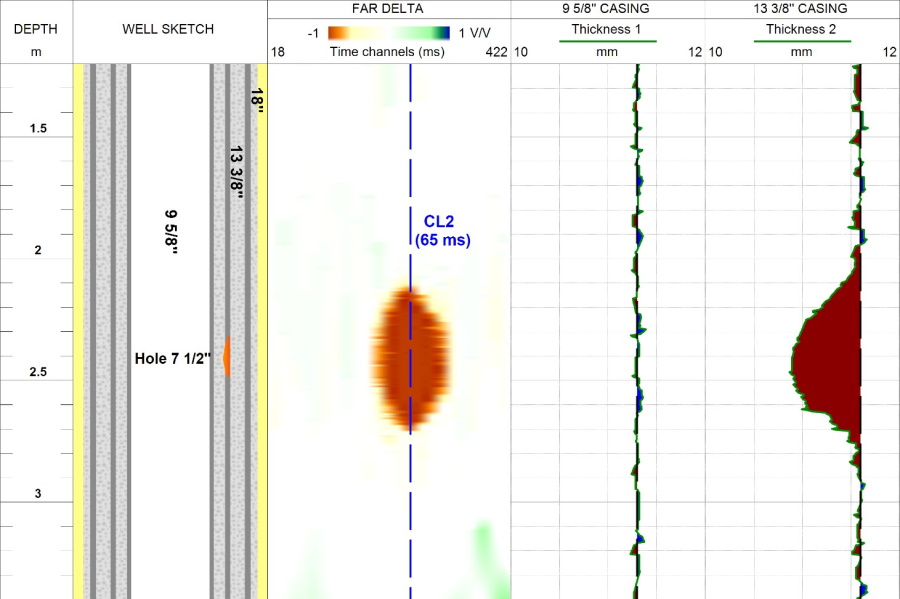 Рис. 5.14. Результаты лабораторных исследований прибором EmPulse-3: (а) дефект во втором барьере трехбарьерной конструкции из труб диаметром 9-5/8", 13-3/8" и 18".
ПРЕИМУЩЕСТВА И ОГРАНИЧЕНИЯ ТЕХНОЛОГИИ Indigo EmPulse Технология Indigo EmPulse основана на регистрации затухания магнитного поля во временной области и моделировании спадов намагниченности, что дает неоспоримые преимущества при анализе многобарьерных конструкций и позволяет правильно оценивать влияние изменения толщины одного барьера на оценку толщины другого. Ниже перечислены преимущества и ограничения технологии Indigo EmPulse. Преимущества:
- Определение толщин стенок каждого из первых трех металлических барьеров за одну спуско-подъемную операцию Основнымпреимуществомтехнологии Indigo EmPulse является то, что отклонения от номинальной толщины стенки и дефекты в металлических трубах могут выявляться и оцениваться одновременно для первого, второго и третьего барьеров. В результате этого исследование трехбарьерной конструкции может быть выполнено за один спуск прибора, что повышает экономическую эффективность исследования и снижает затраты времени на его проведение.
- Присутствующие на стенках труб отложения не влияют на точность определения толщины
Немагнитные отложения внутри труб, такие как соли и парафин, присутствующий в них флюид, а также условия в стволе скважины не оказывают какого-либо влияния на показания прибора EmPulse, что позволяет сэкономить время на подготовку скважины к исследованию и сводит к миниму- му его воздействие на другие проводимые работы и процесс добычи. - Нет необходимости в калибровке по сорту стали или типу конструкции Исследование может проводиться в трубах, выполненных из стали неизвестного сорта. Данное преимущество дает возможность проводить исследования в старых скважинах, документация по конструкции которых утрачена или содержит неверные данные.
- Оценка коррозионного износа труб из нержавеющей стали
Исследования могут также проводиться в устойчивых к коррозии трубах из нержавеющей стали. - Работа в автономном режиме или в режиме считывания данных на поверхности
Прибор EmPulse может спускаться на проволоке или работать в режиме снятия отсчетов на поверхности. Исходя из предпочтений клиента и наличия кабеля прибор можно приспособить к работе в обоих режимах, устранив таким образом проблемы материально-технического обеспечения. Ограничения: Каротаж производится на низкой скорости, с тем чтобы обеспечить достаточный промежуток времени для намагничивания и регистрации откликов от скважинных барьеров. Следует отметить, что низкая скорость каротажа снижает риск прихвата прибора в стволе и перехлестов каротажного кабеля, при этом увеличивается детализация данных и снижается вероятность
получения ошибок, связанных с высокой скоростью спуска. По причине низкой скорости каротажа и значительной протяженности интервала исследования, охватывающего, как правило, весь ствол скважины, продолжительность исследования может составлять от суток и более. - Неспособность провести различие между потерей металла снаружи и внутри трубы
Прибор регистрирует средний отклик от НКТ без различения внутренней коррозии от наружной, в то время как отклонения в толщине могут иметь место как на внутренней, так и на наружной поверхности трубы. При необходимости проведения подобного различия EmPulse может проводиться в сочетании с микропрофилеметрией. - Невозможно определить азимутальную направленность выявленных дефектов Прибор EmPulse последней модификации не определяет азимутальную направленность дефектов, но при этом способен усреднять зарегистрированные оклики по окружности.
- Интерпретация занимает длительное время и требует значительных вычислительных мощностей для обработки данных
Алгоритм моделирования толщины основан на анализе зарегистрированных прибором откликов во временной области. Данный алгоритм является очень сложным и поэтому при использовании этого метода требуются наличие компьютеров с высокопроизводительными процессорами, обеспечивающими точные и эффективные расчеты толщин и потерь металла.
Ссылки
EmPulse White Paper SPE162054 – Memory Magnetic Imaging Defectoscopy SPE169601 – Time-Domain Magnetic Defectoscopy for Tubing and Casing Corrosion Detection SPE176655-MS – Triple-barrier thickness scanning using through-tubing pulse-magnetic logging tool
|